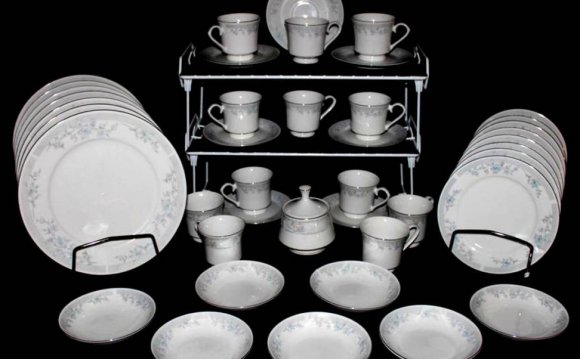
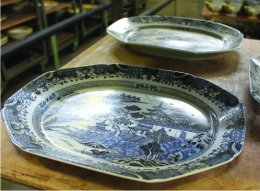
Porcelain is a specific type of ceramic material.
Its main ingredient is Kaolin a naturally occurring ore.Kaolin is a pure white powdery substance that is decomposed granite. When added to elastic, naturally occurring clays, it allows the clay to be fired in an oven at very high temperatures (1900 to 2300 degrees F). During this process the fired clay melts and turns into a glass-like or stone like material and, this process is called vitrification.
Fine porcelain is a white, glassy, and durable material. A fine piece of porcelain is even-colored and blemish-free and, porcelain always contains Kaolin which is granite that has decomposed. When added to elastic, naturally occuring clays, it allows the clay to be fired in an oven at very high temperatures (1900 to 2300 degrees F). During this process, the clay melts and turns into a glass-like or stonelike material. This is called vitrification.
Fine porcelain is a white, glassy, and durable material. A fine piece of porcelain is even-colored and blemish-free. It always contains Kaolin.
Porcelain is commonly known in two forms:
1. Hard Porcelain is a combination of white ball clay, kaolin, and feldspar.
Ball clay has decayed organic material in it, such as ground up dead leaves or plant material. This allows it to stretch so that when the clay is fired it will not crack.
Kaolin allows it to hold together when fired to temperatures necessary to melt it.
Feldspar is a very hard rock and gives the ceramic item strength.
When hard porcelain is fired, it is non-porous. That is, the ceramic is solid all the way through. When water is applied to unglazed hard porcelain, the water will not penetrate it. However, at the high temperatures necessary to melt the clay into a solid, it has a tendency to droop or “slump”. Complex or curvy shapes tend to slump even more. Thus it is difficult to make hard porcelain that is thin and shapes that are not warped. For this reason, the English created bone china.
2. Bone China is composed of the ingredients listed above.
Bone ash allows the clay to be produced thinner and slumping does not occur in the oven. It is possible to make porcelain that is translucent because of this thinness. However, bone china is porous, is fired at lower temperatures and therefore is more fragile that hard porcelain.
Complex or difficult shape, while remaining thin or light.
When hard porcelain is fired, the material is heated so hot that it fuses into a glassy material. At the point that it turns to glass, it also turns to a partial liquid. As the object cools, it solidifies again. It is a fine balance between solid and liquid during the firing process. We want the porcelain to fuse into its future hard state and we don’t want it to sag in the process. It is like baking a cake. There is an optimal cooking time and temperature for a good cake. You want it to turn solid, but you bake it just enough so that it becomes a moist springy cake and not a burned, crispy and unappealing cake.
Getting porcelain to “stand up” in the oven is difficult. If there is little too much heat for too long, you get a droopy bowl. A complex porcelain object is “engineered” to stand up to stress during firing. Understanding porcelain construction uses the same principles governing the construction of a gothic church. The stress points on a piece of porcelain are the places where there is the most pressure during the melting stage when the walls want to give way. These are the points that must be thicker to hold the other parts up, or in the alternative, these points need bracing. To arrive at a new shape or copy an old one, technicians must make a model that may slump, but will slump to an intended shape when the porcelain is finished being fired.
Is the painting vibrant, clear, colorful, gentle, bold, subtle, and timeless? These are the things to look for in beautiful porcelain. Whatever it is, it should be “all-the–way”. The plate or object should represent a style “with conviction.” For this reason, everyone may like something different, but he or she will have feel strongly about the object. The object will be appreciated today and also in 100 years.
When you look at the plate, is the red a strong clear color that looks like glass? Does it have a raised look like an enamel? When you look at the leaves on the plate, are they composed of a blue-green, grey-green, and true green, all in the same leaf, or is it one simple color of green? If the plate has a high price tag, it should meet your expectations for excellence and this should be reflected in bountiful color and delicacy of color, with all its various shades and hues.
For the last 2000 years, until about 1800, porcelain decoration was painted by hand.
Nowadays, 95% of porcelain is decorated with lithography (or silk-screened) decorations.
Instead of using ink, porcelain decorations are created using naturally occurring oxides otherwise considered ground up stone. This is the same material as was used with porcelains of old. The Chinese used ground stone that was rich in metals and they mixed it with water or oil. The same materials are used today, but each piece is not individually hand painted; rather, a series of decorations are printed on paper in the form of water-transfer decals. These decals are applied to fired white porcelain and then fired again. During this glaze firing, as it is called, the decoration is fused to the porcelain as the oxides and glaze melt. The decoration becomes glass. This finished piece has the same quality as a hand painted piece. After this initial decorating process, the porcelain is sometimes decorated again with hand painting. This is usually on the rim or the handles of a piece.